Alright folks, today was one of those deep dive days. Been obsessed with figuring out how the Etruscans made their crazy beautiful jewelry after seeing some museum pieces. Seriously stunning stuff. Wanted to know how they did it, not just look at it. So, I decided to try bringing a few of those ancient tricks back to life in my little workshop. Here's how it went down, blow by blow.
First Step: The Info Hunt (And Why It Sucked)
Figured I'd just search it up, right? Wrong. Typed in "Etruscan jewelry making how to" and mostly got pictures of fancy necklaces and earrings, big surprise. Some fancy museum articles used words longer than my arm – total gibberish to me. Got super frustrating. Had to dig like a mole through old dusty archaeology papers online to find anything useful that actually talked about the making part. Took ages. Ended up with five methods that seemed doable without needing a palace goldsmith's setup: Granulation, Filigree, Repoussé, Casting, and that textured wire stuff.
Gathering the Stuff (My Wallet Cried a Little)
Okay, time to gather gear. Used fine silver wire and sheet instead of the real deal gold cause my budget ain't king-sized. Found my little butane torch, some old charcoal blocks for soldering (works kinda like their old setup, I think?), simple hand tools like pliers and hammers. Hardest part was making tiny solder balls for granulation – seriously finicky! Picked up a punch for the textured wire bits.
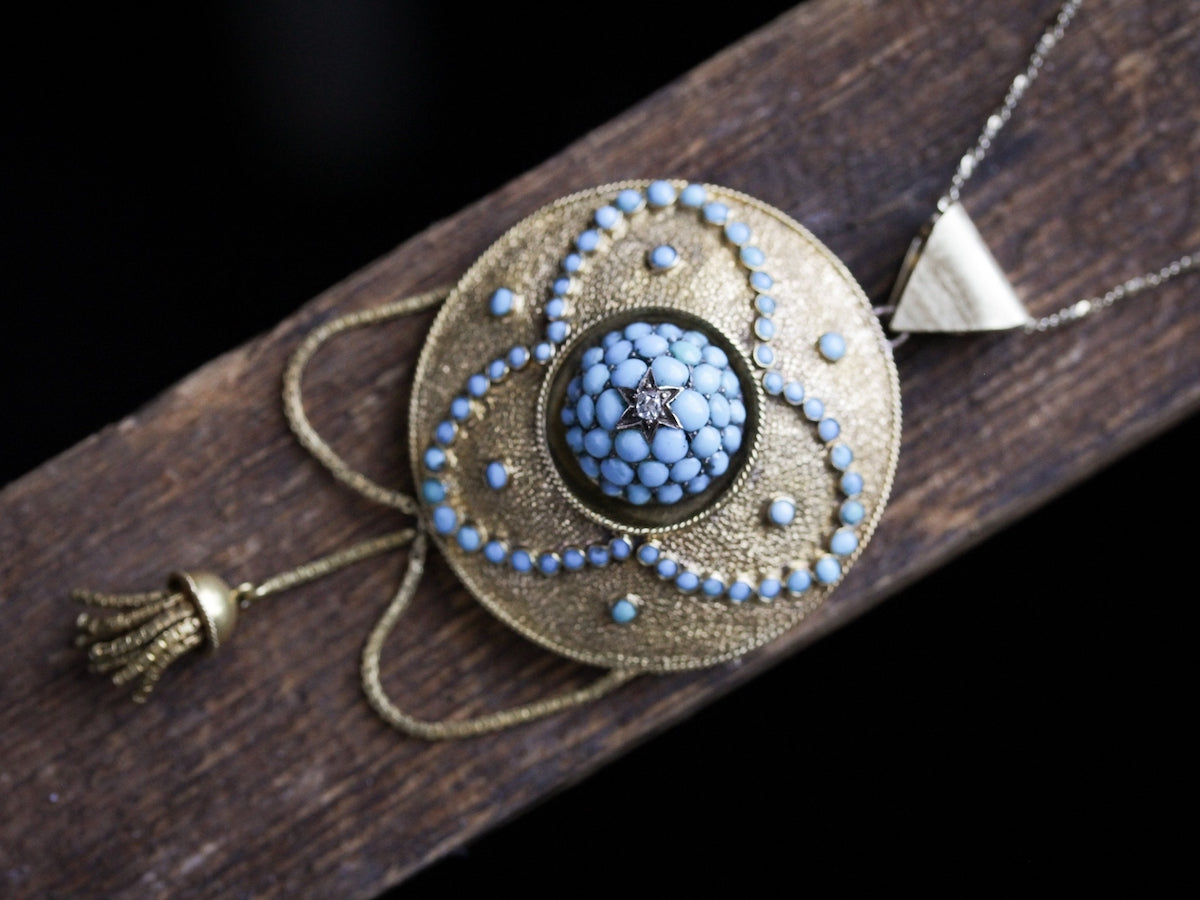
The Actual Doing Part (Full of Oops Moments)
Rolled up my sleeves and started trying things out.
- The Tin Ball Nightmare (Granulation): First up, the famous tiny balls. Tried gluing them onto the silver base plate with store-bought paste solder. Looked easy online. Hah! Placement was like playing operation drunk. Half the tiny buggers rolled off when heating, others decided to blob together into mutant balls. Took three tries just to get a semi-straight line before I even thought about a pattern. Torch control is everything here. Barely pulled off a tiny dot cluster.
- Twisting Tiny Wires (Filigree): This one felt nicer. Took thin wires, twisted some pairs together by hand – not perfect spirals like the originals, but a similar vibe. Laid out a simple curl design on the charcoal block and tried soldering the joins. Keeping the wires still while heating... let's just say there was some mild cussing. Got one corner fused finally. Patience, major patience.
- Poking the Metal from Behind (Repoussé): Took a small piece of thicker silver sheet, taped it face down onto some thick modeling clay. Used a blunt chisel to push out shapes from the back. Forgot how tough thin sheet metal is! Pushed too hard – oops, right through. Started again, lighter taps. Made some simple dome bumps, then flipped it and defined the front edges slightly with a punch. Way more physical than I expected!
- Pouring Hot Metal (Casting - My Messy Try): Used their "lost wax" method in a super simple way. Made a quick clay mold around a small wax shape. Heated up some extra metal bits in a small crucible on the charcoal with the torch. Poured it in... mostly missed the hole. Second try, got some metal in, but it looked like a silver turd. Not winning any beauty contests. Definitely need more practice and better setup for this one. Way harder than it looks.
- Ribbon Wire Texture: This one was oddly satisfying. Took some thicker square wire. Laid it flat and punched little lines across it using a thin chisel point. Flip, punch the other side the same way. Turned it into a neat textured ribbon. Easiest one by far, actually looked pretty cool for edging.
Putting Some Bits Together
Felt brave after surviving the basics. Tried combining the easy bits. Took my bumpy Repoussé piece, added a tiny strip of my textured ribbon wire around the edge (soldering sweat happening!), and attempted to add three lonely granulation balls. Semi-functional! Held together. Not museum quality, but recognizable as a thing I made using their ways. A small victory!
Thinking About It All
Man, those Etruscan dudes were absolute masters. Trying just these five methods showed me that instantly. The detail level they got with basic tools and a hearth fire is mind-blowing. Like, the control needed for perfect granulation patterns? Forget it. My fingers are sore, I used way too much solder, and my casting needs serious work. But just trying it made me appreciate those old pieces so much more. It’s not just shiny stuff; it’s ridiculous skill and patience made solid. Gonna keep poking at granulation, maybe scale it up tiny bit by tiny bit. Those little balls beat me today, but I'm not done yet!